Artificial Intelligence
Challenges and Considerations in Warehouse Management:
Managing a warehouse isn’t easy inventory errors, poor layout, and labor shortages can hurt your bottom line. Learn how I solve these issues with smart tools and strategies.
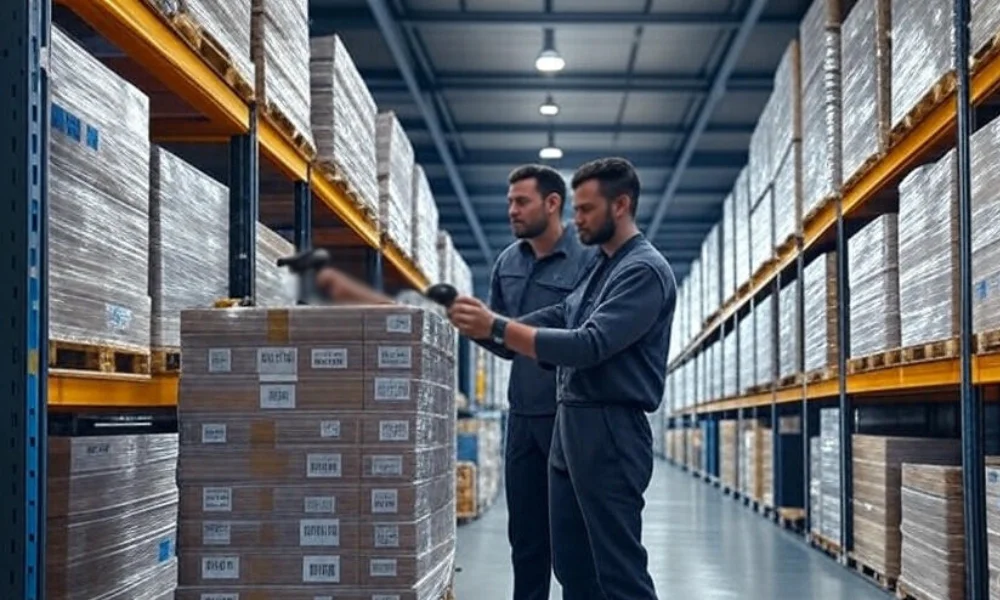
Dealing with warehouse management is harder than before because of growing demands from customers. It is clear to me that even a minor problem in the warehouse can stop the whole supply chain. While storage is part of it, accuracy, speed, and controlling costs is what warehouses are really about.
Definition:
Warehouse management means controlling the inventory, available space, workers, and technology on a day-to-day basis in a storage facility.
I wanted to write about these matters in order to help businesses do better by managing warehouse operations. I’ll cover everything about inventory management and employee safety.
Common Warehouse Management Challenges:
Running a warehouse means supervising not just the arrange of things but also accuracy, staff, and various tasks in real time. I have dealt with issues that result from system failures or from poor planning being carried out. We should look at some of the usual warehouse challenges and how they have an effect on operations.
Inventory Inaccuracy:
Problems with inventory have sometimes caused sales to be canceled, order delays, and customers who are unwilling to go back to the company. Most of the time, gaps happen when someone enters the wrong product details, mislays some items, or waits too long to update stock records.
If the stock levels are off, this causes challenges for both warehouse workers and customer service agents. It ruins organization with customers and keeps them from having a positive experience with warehouse services.
Why Does Poor Space Utilization Hurt Productivity?
In a busy warehouse, I can tell that lack of space becomes a major challenge instead of something useful. Not using all the available space in your warehouse may mean picking is inefficient and workers have to look for goods for longer.
A number of warehouses have plenty of space, but others are full, making work less efficient and adding risks. Proper planning of the layout saves your time and ensures that each location in the warehouse is being used.
How Do Labor Shortages Impact Warehouse Efficiency?
It is tough to find people today who are familiar with warehouse tools and systems. Sometimes, racial barriers have made it hard for temp workers to get the training they need to handle the busiest times in the store.
Managers deal with even more stress because they have to repeatedly train new employees. If the team is not steady, how quickly you can pack will decline and there may be more mistakes in your orders.
Inefficient Processes:
I have seen that some warehouses, both small and mid-sized, still do things the manual way in certain functions. They decrease productivity because paper logs or isolated systems make it difficult for workers.
The process of packing or shipping products slows down, so the business is unable to fulfill its orders on schedule. If we were to use technology to solve these problems, we should plan and invest properly.
Why Is Real-Time Data So Essential?
Because I couldn’t track my products in real-time, many of my decisions ended up regretting. Lagging updates to the data cause stores to have too much stock, too little stock, and uncertainty during the restocking process.
Managers in warehouses should be able to see live updates about everything. Relying on old information results in wasting cash and time that are both lost.
What Are the Risks of Equipment Downtime?
A sudden breakdown of a forklift or conveyor belt during a shift usually leads to everything coming to a halt in the warehouse. Mishaps like that cause deliveries to be late and put extra pressure on workers, increasing their hours.
Preventative schedules are often disregarded since most people find them inconvenient. Procrastinating repairs can result in greater damage than just the amount you will pay to fix things.
Order Accuracy Issues:
There was a huge rise in returns for me because workers chose the wrong piece or item. If an order was not correct, it brought about costs in refunds and reshipping, and at times it also meant losing that customer’s business.
Order accuracy depends on labeling, scanning, and training. Without it, even fast shipping won’t make up for mistakes.
Key Considerations for Effective Warehouse Management:
It’s not enough in logistics to simply solve problems; good warehouse management means setting flexible and sturdy systems. I’ve figured out the base aspects that can stop issues from emerging. I would like to share the factors I always keep in mind while designing or optimizing a warehouse plan.
Warehouse Layout and Design:
How the warehouse is organized will impact all activities and I can see that a good design cuts down on time spent in the warehouse. With a good plan, workers walk less, orders arrive sooner, and things are handled only once.
It also greatly helps in increasing both productivity and safety. Things that move quickly should always be close to the packing area, whereas bulky items need to be stored separately.
How Can Technology Improve Warehouse Operations?
A good Warehouse Management System (WMS) changed the game for me. Because of it, I was able to automate handling stocks, diminish mistakes, and be much more accurate. Because of barcode and RFID technology, fewer mistakes are made during scans and more time is saved per shift.
AI and robots are the key to warehouse operations in the future, and they have lowered the need for people. They allow workers to complete the sorting and picking tasks faster.
Why Is Staff Training and Safety Non-Negotiable?
I always focus on training—having trained employees leads to less mistakes and better handling of tough shifts. I keep my training updated once every three months when additional systems or tools become available.
Staying safe should not be left behind. Wearing the necessary PPE and following other OSHA standards not only avoids accidents but also makes insurance costs lower and workers more motivated.
Scalability and Flexibility:
All warehouses I’ve been involved with have had to deal with changes in the amount of work during different seasons. I arrange for designs that can handle extra storage, putting mobile shelving and racking on standby. This way, things don’t get disorganized in months when tournaments are more common.
Flexibility helps during slow seasons too. Dynamic slotting lets me move products around easily without major disruptions or downtime.
How Do I Keep Warehouse Costs Under Control?
The first thing to do with cost control is to find out what is truly of value. I always ensure that the time and money used for tech upgrades or rearrangement will be worthwhile. Spending money should assist in increasing speed, making sure tasks are done accurately, or satisfying users.
I pay attention to extra costs such as leftover packaging, space that goes unused, or overtime people work. Making cuts without harming the services you provide will help you save money for the long run.
Why Should Warehouses Go Green Today?
Being sustainable has become a smart business move, apart from doing something good. I rely on LED lights, motion sensors, and highly efficient tools to help lower my energy spending. The return on investment happens quickly.
If we use less packaging, that is also helpful. I create lasting relationships with suppliers so we avoid extra waste and use containers more than once.
Is Third-Party Logistics (3PL) a Smart Move?
I rely on 3PL partners to support me whenever I enter new markets or expand very quickly. Thanks to outsourcing, I did not need to add more workers or find additional office space. I was able to use fewer fixed expenses because of it.
Nonetheless, I take time to examine each 3PL before forming a partnership. A struggling partner may create issues for customers that lead to late shipments or errors in handling goods.
Industry Examples & Case Studies:
The things I learn from successful projects around me influence the strategies I build for my warehouse. I always consider the successful actions of others and how they gauged their accomplishments. Here are two situations that make it clear how easy progress can be bad for the environment.
How a Retail Warehouse Reduced Errors with RFID?
There was a retailer I watched, and they often had problems with their inventories, which disappointed customers and destroyed their brand’s image. RFID tags were used by the management team to keep track of all goods the minute they arrived at the warehouse.
In only three months, they managed to reduce picking mistakes by more than 60% after putting RFID scanners everywhere. Things were found by the staff faster, and managers always knew what was happening with inventory.
The firm also took advantage of real-time information to fine-tune its stock replenishment and deal more effectively with seasonal changes. RFID not only decreased mistakes, but it also made the whole process smoother.
How an E-commerce Brand Doubled Its Picking Speed with a New Layout?
A retail company I admire experienced problems with fast order fulfillment and as a result, customer numbers remained low. The items stored at the warehouse were not well arranged, so pickers spent more time traveling through the aisles.
They looked at selling trends and changed the layout to focus on frequently bought items and hot products. This design improvement resulted in moving the fast-moving products near the packing areas.
For this reason, their pickers spend only half the time they did before, and the amount of orders they handle each day has doubled. The faster shipping pleased customers, which resulted in better feedback and added return buyers.
Future Challenges in Warehouse Management:
As someone involved in logistics, I’ve realized that the future of warehouse management comes with new complexities and unexpected shifts. To stay competitive, I know I must prepare for changes before they disrupt operations. Let’s explore what lies ahead and how I plan to adapt.
How Will E-Commerce Growth Reshape Warehousing?:
E-commerce keeps growing fast, and I’ve seen it push warehouses to their limits with rising order volumes every year. This shift means higher expectations for speed, accuracy, and 24/7 fulfillment across multiple platforms.
I must plan for more automation, tighter picking zones, and micro-fulfillment centers near cities. These changes support faster delivery without sacrificing accuracy or increasing labor demands.
Will Automation and AI Replace Warehouse Workers?
Labor costs and shortages already push me toward automation, but I still need trained people to manage and operate smart systems. AI tools help with demand forecasting, inventory allocation, and predictive maintenance, freeing me to focus on growth.
Still, I see the risk of over-relying on machines. I make sure training and human oversight remain part of every automation decision I approve.
How Do I Prepare for Global Supply Chain Uncertainty?
After what I saw during COVID-19 and other disruptions, I no longer assume steady supply chains. I diversify vendors and keep extra stock of critical products, even if it means higher short-term costs.
I also use real-time data to spot slowdowns early and shift orders as needed. Planning for uncertainty helps me reduce risks and respond with confidence.
Conclusion:
Managing a warehouse today means more than just stacking boxes and shipping orders, it’s a balance of precision, speed, and strategy. I’ve faced issues like inventory inaccuracy, space waste, and slow workflows that impacted my overall efficiency.
Through smart planning and the right tools, I learned to turn those challenges into opportunities. Better layouts, advanced systems, and real-time insights helped me improve order accuracy and team performance every quarter.
But I know this journey never stops. I continue to update my skills, adopt new tech, and learn from other successful operations across the U.S. warehouse landscape.
If you’re managing a warehouse, stay flexible and never stop refining your processes. Change is constant, and success depends on how well you adapt.
What challenges are you facing in your warehouse operations? Let’s start a conversation. Your insights could help someone else improve their own process. Drop a comment or share this post if it helped you today.
-
Artificial Intelligence8 months ago
What is Artificial Intelligence? A Comprehensive Guide for Businesses and Enthusiasts
-
Artificial Intelligence6 months ago
How to Use Grok AI: A Complete Guide
-
Artificial Intelligence8 months ago
Unlocking the Power of Artificial Intelligence Tools
-
Artificial Intelligence7 months ago
What is DeepSeek? Revolutionizing AI with Cutting-Edge Solutions
-
Artificial Intelligence3 months ago
AI Technologies in Warehouse Automation:
-
Artificial Intelligence4 months ago
Meta’s AI Push: The Standalone Assistant App Set to Rival ChatGPT
-
Artificial Intelligence3 months ago
How Artificial Intelligence is Revolutionizing Logistics:
-
Artificial Intelligence3 months ago
Predictive Analytics for Demand Forecasting: